ROCOL expert Chris Dyson answers your questions on anti-seize. Let’s start at the beginning…
What is Anti-Seize?
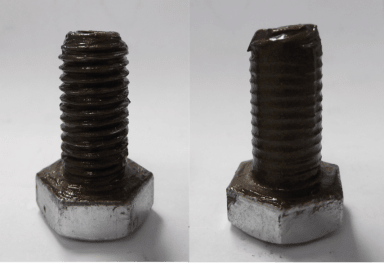
Anti-Seize expert, Chris Dyson, answers some frequently asked questions that arrive at our tech desk.
1. What is Anti-Seize?
Anti-seize products are applied to bolts, fasteners, flanges and other clamped interfaces to prevent galling, seizing and corrosion, as well as lubricating to ease disassembly.
Anti-seizes can be pastes, greases and coatings, and they can be based on a wide range of materials (e.g. copper, nickel) to suit particular systems. Therefore, the selection of the correct anti-seize product for the particular system is crucial. A selection guide is available
2. Why use Anti Seize?
A properly chosen and applied anti-seize can produce a wide range of benefits to an engineering system. Anti-seize can:
• Prevent pick-up and galling of fasteners during assembly
• Produce a more precise and consistent clamping load in fasteners
• Separate and lubricate the surfaces of a jointed interfaces during operation, reducing wear and loosening
• Reduce corrosion of interfaces by preventing water ingress and chemical attack
• Ease dismantling and prevent damage to components during disassembly
Some anti-seize products are designed for dynamic systems.
These can:
• Assist the assembly of interference fits
• Reduce fretting wear of components in vibrating systems
• Reduce friction and wear of mated surfaces with relative motion e.g. splines, couplings
3. Where should Anti-Seize be Applied?
Essentially, when required, a thin layer of anti-seize should be applied to each interface in an assembly. This should ensure the best protection of the interfaces in the system.
When anti-seize is being used on a fastener assembly, it should be applied to the following surfaces:
• The thread of the bolt or stud
• Plain, unthreaded sections of the bolt or stud if they will be inside the assembly
• The face under the bolt head
• The nut face
• All parts of the washer if one is used
A thin layer is sufficient – Any excess will be squeezed out during tightening.
4. How much Anti-Seize should be Applied to a Surface?
A thin layer is sufficient. For a typical fastener assembly, a film approximately 0.1mm thick is suitable.
Some guidance recommends completely filling thread valleys of a bolt with anti-seize. However, as excess anti-seize is squeezed out under tightening, this quantity is excessive and often wasteful. A thin layer is recommended.
With an aerosolized anti-seize, the instructions on the Technical Data Sheet explain the best way to achieve a thin layer with uniform coverage.
However, the specific conditions in each system should be considered. The ROCOL technical team can advise on this
5. What is the Best Method for Applying Anti-Seize to a Surface?
Before application, ensure that surfaces are clean and free from oil, grease or contamination, especially if components are supplied oiled.
For the application of a thin layer of anti-seize, a brush is normally most effective. Using a brush will produce a more even layer than using a gloved hand/finger, especially on threads.
A brush should be used for one material only. If a brush has been used to apply a particular anti-seize compound, it should not be used to apply another, even if cleaned. Cross-contamination can affect performance.
For an aerosol spray, following the instruction on the can and the Technical Data Sheet should produce an even layer of anti-seize on component surfaces.
6. How Should a Surface be Prepared before Applying Anti-Seize?
For the best results, surfaces should be clean, dry and free from oil, grease or contamination. This can be achieved using a residue-free industrial cleaner such as such as ROCOL Industrial Cleaner Rapid Dry
Many nuts and bolts are supplied oiled to prevent corrosion in storage. It is recommended that any oil is removed before application of an anti-seize, so that it cannot affect the frictional properties of the anti-seize (then the bolt tension) or the corrosion resistance.
7. Does Anti-Seize Need to be Reapplied?
Anti-seize compound is not like a bearing grease or gearbox oil in that it isn’t necessary to periodically replace it. Once applied, it is designed to last for the service interval of the interface.
However, if a fastener is disassembled or an interface is parted, it is recommended that the components are cleaned and anti-seize re-applied.
If fasteners are re-tightened or reused, caution should be used when choosing the torque settings. Because the surfaces of fasteners change as they are deformed under load, the coefficient of friction may not be the same the second time a bolt is used – Which might affect the final tension.
8. How Should an Anti-Seize Compound be Removed from a Surface?
For cleaning an anti-seize compound from a component, a standard industrial degreaser (e.g. ROCOL Heavy Duty Cleaner or Remover & Degreaser Spray ) or solvent cleaner (e.g. ROCOL Industrial Cleaner Rapid Dry or Electra Clean) should be suitable. A brush or rag should be sufficient for the cleaning process – Abrasives are not recommended as they will damage component surfaces.
It is important to leave the surface in suitable condition for the next stage of its life:
• If a clean surface is required afterwards, a residue-free cleaner such as ROCOL Industrial Cleaner Rapid Dry or Electra Clean.
• If the component will be stored, a corrosion inhibitor may be required to protect the surface e.g. ROCOL Moisture Guard, Z30 or FOODLUBE Protect.
Find out which anti-seize system is the best for you!